Posted on Aug 1, 2020
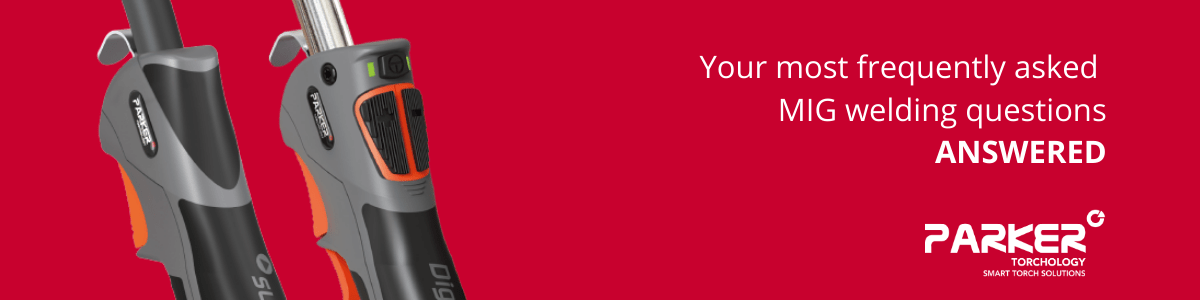
We’ve been manufacturing for the welding industry for decades, and we get asked questions about Mig welding all the time. Here are few of the most frequently asked questions, answered!
Why Use Mig Welding?
Mig welding torches are the workhorse of the welding world. One of the easiest processes to learn, ideal for a wide range of applications and suitable for a wide range of metals including steel, stainless steel, carbon steel, aluminium and other alloys, Mig welding offers versatility and productivity.
How Does Mig Welding Work?
Put simply, Mig welding works by creating an electrical arc between a wire and the metal being welded. This arc melts the electrode wire which forms the weld. The welding wire is fed constantly through the torch, which allows the welder to work without constant stop/starts. Gas (usually Carbon Dioxide, Argon or a mix) is also fed through the welding torch, which protects the area being welded from atmospheric gases which can cause weakness in the weld.
Air-Cooled Or Liquid-Cooled?
This decision is usually down to application requirements. Liquid-cooled Mig welding torches allow the welder to weld repeatedly at higher amperages. Air-Cooled Mig torches would not be able to handle the heat that this would generate. On the other hand, if the operator only needs to weld a few minutes every so often, Air-Cooled would likely be sufficient. Liquid-Cooled Mig setups are usually more costly, both upfront and in maintenance and operation, but are ideal for stationary applications where higher amperages and operation levels are required, offering real productivity benefits. Air-Cooled Mig welding allows more portability, and probably most importantly, lower costs.
What Amperage Do I Need?
Selecting the right torch for the job is key to ensuring that the torch does not overheat. Welding torches typically have a duty cycle listed, which shows how many minutes in a 10 minute period the torch can be operated at that capacity. Eg 150A @ 60%, would mean that the torch could be used at 150A for 6 minutes in every 10. If the welder is not going to be using the torch at its full capacity, they may be able to use a smaller, lower amperage torch. For example, you may be able to use a 300A Mig gun instead of a 400A since the actual arc-on time does not exceed the amperage to duty cycle ratio of a 300A gun.
Another consideration is the gas used. Duty cycles are usually given with CO2 used as the shielding gas. Use of any other gases or mixes will reduce the duty cycle.
What Torch Style Should I Use?
Design is often a personal decision for a welder. They may have learnt with a particular style or become accustomed to a handle shape and trigger location. With so many different variations available as well, it can become complicated. The important thing to remember is that, while you can to some extent, adopt a one-size-fits-all approach, you may find that you at least need to use different consumables to ensure the quality of your weld in different scenarios. You may also require a more specialist torch for a particular job.
For applications such as tacking or sheet metal welding which require short welding times, a smaller, lightweight, lower amperage torch is ideal. they are generally cheaper as well. Plus, the lightweight makes them more comfortable to work with and improves manoeuvrability.
Larger, heavy-duty torches are suited to jobs on thick metals, and where multiple passes and long welding times are required.
Longer necks distance the welder from the weld and the high heat output, while shorter necks can aid with precision.
Our team are always on hand to support with help and advice on selecting the right Mig torch and consumables for your needs.